Digitální transformace je otázkou přežití českého průmyslu
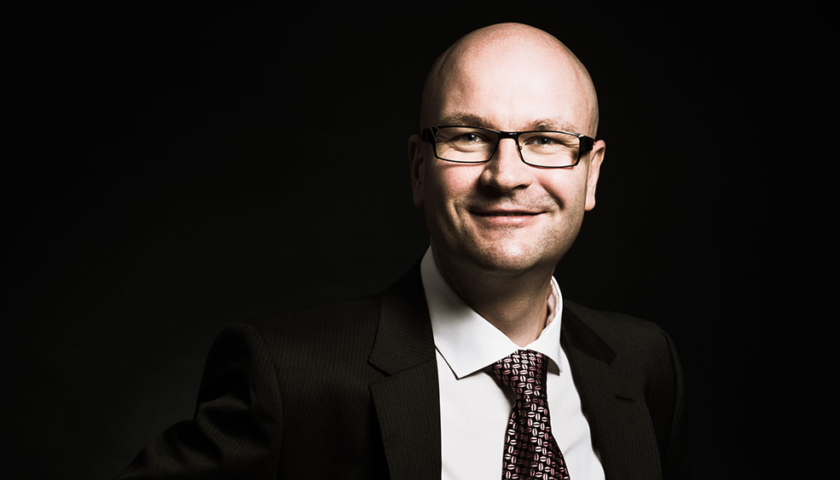
Zavádět digitalizaci výroby znamená mimo jiné přemýšlet o budoucnosti. Tu určují především velcí světoví hráči. Jaký koncept digitalizace pro budoucnost tvoří firma Siemens detailně vysvětluje Tomáš Duba, ředitel jednotky Motion Control v této společnosti.
Představme si moderní automatizovanou linku, představme si celý proces výroby krok po kroku a podívejme se, jak může digitalizace zvýšit úspěšnost každé fáze.
Jaké nástroje Siemens nabízí pro rychlé spuštění výroby a optimální sestavení výrobní linky?
To začínáme od konce (smích), protože spuštění výroby je z pohledu celého výrobního cyklu až jedním z jeho posledních kroků. A aby spuštění výroby proběhlo úspěšně a v co nejkratším čase, je podle mě nejdůležitější, aby došlo k názorovému průniku mezi dodavatelem technologie (výrobcem linky) a jeho budoucím uživatelem (koncovým zákazníkem). Pro uživatele není snadné správně definovat svoje představy a nároky na nové zařízení. A stejně obtížné může být pro výrobce technologie tyto požadavky pochopit. A tady už nám do popředí vystupuje digitalizace. K tomu, aby si výrobce a budoucí uživatel co nejlépe rozuměli, se perfektně hodí digitální dvojče. A ne jedno, ale hned tři.
Dobrá, které je první?
Středobodem všeho je digitální dvojče výrobku. Představme si například dron, který řada z nás používá k filmování krajiny. Co asi předcházelo tomu, než se nám dostal do ruky? Když chci vyrobit dron, musím začít s návrhem výrobku a vytvořením jeho digitálního dvojčete. Tím nemyslím 3D model v CAD systému. Pro úspěšné uvedení nového typu dronu je třeba začít s optimalizací jeho návrhu včetně simulací chování v reálném prostředí, a k tomu slouží jeho digitální dvojče. Jedině tak máme možnost odzkoušet jeho budoucí letové vlastnosti při simulaci proudění (obtékání vzduchu), mechanického i tepelného namáhání. Díky této simulaci a optimalizaci může dojít k úpravě jeho topologie. Pokud bychom začali rovnou s plánováním výroby a přeskočili návrh a optimalizaci výrobku, výrazně bychom omezili budoucí vlastnosti dronu. Výrobní technologii je totiž třeba navrhnout až v souladu s navrženými materiály a jejich rozměrovým uspořádáním. Může se totiž stát, že zvolíme tak progresivní profil dronu, že nepůjde vyrobit standardními technologiemi. Třeba výrobu vyřešíme 3D tiskem z kompozitních materiálů, anebo se budeme muset o krok vrátit a změnit návrh.
Produkt máme navržený a odladěný. Co dál?
Teď se můžeme posunout k digitálnímu dvojčeti výrobního stroje, linky nebo i celé továrny. Princip je pořád stejný, liší se pouze škálovatelností. Podle digitálního dvojčete výrobku začneme navrhovat a optimalizovat výrobní proces. Výsledkem je digitální dvojče výrobního stroje, které šetří jeho výrobci nemalé náklady s uvedením do provozu. Může si totiž odsimulovat chování samotného stroje ještě dávno předtím, než se pustí do jeho fyzické výroby. Každá případná chyba v konstrukci stroje je odhalena a opravena ještě ve virtuálním prostředí. To vede ke zkrácení nového výrobního stroje na trh až o 30%.
A co třetí digitální dvojče?
Pro úspěšné spuštění každé nové výroby v co nejkratším čase a s co nejnižšími náklady, je potřeba ještě digitální dvojče výroby. Teprve potom se celý kruh třech digitálních dvojčat uzavře. V podstatě spustíme virtuální výrobu bez toho, že bychom ještě kopli do země a začali budovat novou výrobní linku. Vezmeme totiž digitální dvojče výrobku, vložíme ho do digitálního dvojčete výrobního stroje či celé linky a spustíme digitální dvojče výrobního procesu. Virtuálně vyrábíme virtuální výrobek na virtuálním stroji, to má ale svůj obrovský význam. Díky tomu všemu koncový uživatel, který je zároveň i investorem, má absolutní jistotu, že kupuje výrobní technologii, která přesně vyhovuje jeho potřebám. Ba co víc, může si nasimulovat výrobní časy, takt celé výrobní linky, použité přípravky, nástroje a energie a díky tomu si spočítat návratnost své investice. To už dává smysl, ne?
Zejména při náběhu výroby je důležitá kontrola kvality, jak je Siemens připraven na tuto fázi?
Pokud máme všechna tři dříve popsaná digitální dvojčata, není nic snazšího. Digitální dvojče je totiž etalonem, ke kterému se vždy můžeme vrátit a měřit odchylky reálného prostředí vůči ideálním hodnotám digitálního normálu. Podle trendu růstu těchto odchylek jsme schopni sledovat, co se s naší výrobní linkou děje, a díky tomu i včas zasáhnout. To má dvě roviny. Jednak úhel pohledu skrze vlastní výrobu: sledujeme dodržování výrobních postupů, kvality výroby i kvality vyráběného produktu. Druhý úhel pohledu je zaměřen na výrobní stroj či celou linku. Monitorujeme kondici naší výrobní technologie. Měřením odchylky vůči digitálnímu dvojčeti výrobního stroje máme přehled o stavu stroje. Dokážeme předvídat vznik možné poruchy a díky tomu i včas zasáhnout a předejít výrobním prostojům a vzniku škod na stroji.
Linka běží a všichni usilují o co nejkratší cyklové časy. Co nabídnete pro zvýšení rychlosti výroby?
Uzavřením kruhu výrobního cyklu se ocitáme opět na začátku a můžeme přistoupit k nové optimalizaci. Jednoduše vezmeme aktuální výrobní data a použijeme je jako vstupní údaje pro opětovnou optimalizaci celého výrobního cyklu. Dostaneme tím tak nikdy nekončící proces permanentního zlepšování kvality výrobku samotného, tak i jeho výrobních nákladů a časů. Pokud například koncový uživatel provozuje stejné výrobní linky na různých kontinentech, může použít data z jedné lokality ke zlepšení parametrů výroby všech ostatních závodů. Díky tomu zlepšovací proces ještě silněji akceleruje. Bez digitálních dvojčat by bylo nesmírně těžké určit, co je optimální stav a jaké korekce přijmout, abychom se k němu rychleji přiblížili.
I když prediktivní údržba vyřeší mnoho problémů včas, vždycky se může stát, že dojde k nečekané poruše. Jaké digitální nástroje Siemens nabídne pro rychlý servis?
Nabízíme vzdálený servis, kdy výrobce stroje na svém digitálním dvojčeti simuluje poruchu, která vznikla v reálním prostředí u koncového uživatele. Výrobce linky tak ve svém zázemí pracuje na opravě stroje, který je přitom fyzicky nainstalován třeba na opačné polokouli. Je to podobné jako příběh Apolla 13, které zavolalo: „Houstone, máme problém!“ a Houston problém vyřešil.
Aktuálně jsou velkým tématem energie, máte nástroje k jejich sledování a snižování?
Nástroje na sledování spotřeby energie, optimalizaci výroby a tím i jejich snížení samozřejmě máme, a to napříč celým portfoliem. Já bych se ale raději vrátil na začátek našeho rozhovoru k příkladu dronu. Pokud budeme optimalizovat návrh výrobku s ohledem na efektivitu jeho vlastností a produktivitu jeho provozu, můžeme ušetřit ve výsledku mnohem více než pouhým monitorováním naší stávající výrobní technologie ve snaze snížit její spotřebu energií.
Navrhujete tedy jít jinou cestou?
Mojí odpovědí je neustálý proces inovace výrobního cyklu a investice do nových pokrokových technologií a samozřejmě do kvalitních zaměstnanců. Na ty samozřejmě nesmíme zapomínat, protože i ta nejmodernější technologie se neobejde bez zapálených lidí, kteří se nebojí riskovat nové a nezažité postupy. Stojíme před mezigenerační obměnou, protože střední věk technických pracovníků se neustále zvyšuje. Přitom technické školy, učiliště a univerzity mají možnost nabídnout přesně to, co tak zoufale chybí řadě dnešních firem v průmyslu. Tedy šikovné techniky, kteří jsou otevřeni novým postupům, přemýšlejí kriticky a mezioborově se orientují i v oblasti IT.
Je už v nějakém českém závodě toto všechno zavedeno? V jaké fázi digitalizace náš průmysl teď je? Kdy například odhadujete, že budou všechny zmíněné nástroje běžným standardem pro každou firmu?
Samozřejmě máme a velmi rádi a často v těchto závodech pořádáme odborné semináře, abychom mohli našim zákazníkům v praxi ukázat, co jim digitální transformace může přinést. Zmínil bych zde především takzvanou Digitální arénu v závodě na výrobu servomotorů v Bad Neustadt v Německu. Ale také naše české závody na výrobu motorů v Mohelnici a Frenštátě jsou digitalizační výkladní skříní. Co se týká data masové implantace napříč průmyslovými podniky v České republice, zde je to mnohem složitější. Za každou transformací totiž musí stát jasná a dlouhodobá vize managmentu, ze které se neslevuje ani po překážkách, které se během implementace vyskytnou. A to mi ve většině průmyslových podniků zcela chybí, i když světlé se výjimky se samozřejmě najdou. Protože jsem založením optimista, řekněme, že masové nasazení čekám do dvou let. Je to otázka přežití našeho domácího průmyslu.
Foto: Siemens